The day before I was going to speak at Libertopia, an engineer and writer named Michael Eliot came over and plunked a cube on the table in front of me.
“Geopolymer concrete. It should last hundreds or thousands of years in seawater.”
I was so excited I asked Michael Eliot to write up a report, and he delivered “The Case for Geopolymer Concrete in Seasteading,” which we’re proud to publish on our website. It’s such a fascinating read, I had to follow up with a podcast interview.
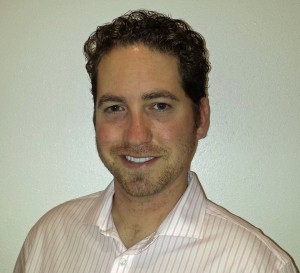
We think Michael Eliot’s paper and podcast will spark productive discussion on our new improved forum. Mike is adept at answering questions at any level of understanding.
He writes, “I have quite a collection of source papers and references by now, the best of which may be the US Airforce investigation of geopolymer concrete for their own use. If you have any questions about claims made please don’t hesitate to ask. I will update you with results of the ocean-endurance tests in the months to come.”
Join the forum, and let’s build seastead prototypes!
For Seasteading,
Joe Quirk, Seavangelist
Want to help seasteading? Please make a donation today and support our forums, operations, and Floating City Project.
Podcast: Play in new window | Download
Sounds like “solving a imaginary problem” that nobody in marine concrete engineering really has….
The reason why nobody is looking for a “new material” is because the existing and proven material is doing a excellent job in long service life (200 years and beyond) anyhow…
Introduction of a basic marine engineering book:
Concrete has clearly emerged as the most economical and durable material for the building of the vast majority of marine structures. Reinforced concrete too has overcome the technological problems making it a suitable material for the construction of advanced marine structures such as offshore drilling platforms, superspan bridges and undersea tunnels. As the world becomes increasingly ocean-oriented for energy and other resources it is predicted that construction activities during the 21st century will be dominated by concrete sea structures. The performance of concrete in the marine environment is presented here in a logical manner giving state-of-the-art reviews of the nature of the marine environment, the composition and properties of concrete, history of concrete performance in seawater, major causes of deterioration of concrete in the marine environment, selection of materials and mix proportioning for durable concrete, recommended concrete practice and repair of deteriorated marine structures. It is of value to any design or construction engineer responsible for marine structures.
Seems to me that the previous comment by “ellmer” or “yook3” (tawny ways to remain anonymous) come from a place and mindset of “if it ain’t broke, don’t fix it”. The horse and buggy wasn’t broken, why go so far as space flight? And cheers to all the fine moments of design and brilliant forward thinking in between. I won’t waste time throwing out literature and quotes to support the notion that all design can be better, I don’t need to.
Actually the Horse and Buggy were broken—consider the state of societal organization at the time automobiles were designed—–then consider the amount of natural horse product that would be mounded up transferring freight at todays volume from city to city—trucks, trains, ships prove the brokenness of the horse and buggy
Geopolymer offers the following potential advantages over traditional concrete:
The main disadvantages are that it requires heating to reach maximum cure strength, and relies on strong alkalis to activate the polymerization process.
It is of interest to seasteaders because we want to create “real estate” that will last centuries with little maintenance. Roman concrete, an ancient geopolymer, has lasted thousands of years in marine environments, so the modern variants are worth exploring.
Incidentally, a lot of development has already gone into geopolymers, and they are already being used in production. For example, Murray & Roberts used geopolymer to resurface the world’s largest inland port, Transnet’s City Deep Container Terminal in Johannesburg, SA.
http://www.murrob.com/news_pr_Detail.asp?id=2522
It is all very well to figure out cost and construction on paper but nothing takes the place of empirical testing. Slip-forming is not a new concept and weight of your solid geo-concrete would seem to be a very real problem. Many of these concepts that are talked about here are not new and patents have existed for many years. It would be interesting to see if production could be realistically achieved. I believe your costs will be in training and implementation of your concepts and they will be much higher than is presumed. President, Laminated Concrete Inc.
Some things to consider when building with geopolymers.
https://www.youtube.com/watch?v=3QGUCHt0tDs
Comments are closed.